
This article is dedicated to innovations in the construction industry. It elaborates on the main trends, provides real-life construction technology examples, and explains their benefits for businesses.
For example, VR training simulators like Onix’s VR/MR app and other innovations in construction safety training make it more accessible and cost-efficient.
Example of educational technology used in construction industry – Onix’s VR/MR safety training app
More and more companies realize the importance of innovation amongst rising costs, labor shortages, evolving sustainability and safety requirements, and other recent trends in construction. Those who adopt the right innovative construction technology faster will be best positioned to create value and maintain a competitive edge.
We have analyzed the latest construction technology trends and distilled five key areas to address in 2025:
- Building site monitoring and construction tracking
- Communication, collaboration & project management
- Advanced use of data
- Virtual design and construction methods
- Immersive technologies in back offices and in the field
(As a software development agency, we are primarily interested in digital construction technology trends, which leaves new construction technology like 3D printing or living building materials out of this article’s scope.)

Ready to develop a construction app and need expert help?
5 Digital Technology Trends in the Construction Industry in 2025
1. Technology for Building Site Monitoring and Project Tracking
Tracking what happens in the field has always been essential for keeping projects on schedule and within budget, mitigating risks, and avoiding costly rework. The shift towards higher efficiency, safety, and sustainability calls for better construction oversight and control.
This drives the integration of Internet of Things (IoT) devices, wearables, drones, robots, computer vision, and other emerging technology trends in the construction industry.
These solutions connect people, equipment, processes, and information and provide real-time data for precise project tracking and increased safety at construction sites.
For example, IoT sensors enable companies to track machines, spot equipment malfunctions and hazards in real time, and get insights into the structural integrity of buildings.
The application of artificial intelligence (AI) and machine learning (ML) helps identify potential issues before they escalate and enable real-time support and corrective actions.
Learn more: AI Agents: Examples, Use Cases, and Development Basics
Onix based its drone and satellite AI solution for mapping and geographic information systems (GIS) on computer vision, object detection, image segmentation, and image processing.
The system detects buildings, roads, rivers, forests, and fields, recognizes their characteristics, and puts them on a map. The solution can also detect changes by comparing the maps with previous observations.
Onix’s mapping and GIS solution creates maps based on images from drones or satellites
5G becoming more accessible and widespread will further facilitate the adoption of mobile technology in the construction industry. Together with Wi-Fi 6, it will enable users to run resource-heavy apps without compromising speed and performance.
Forward-looking construction companies also invest in mobile apps that facilitate real-time data collection, time tracking, field reporting, and communication between on-site employees and back office project managers and enable other new technology in building construction.
Learn more: Construction Application Development – A Step-by-step Guide
Onix has also contributed to this innovation in construction. For example, we once rewrote a mobile app for an American company specializing in luxury housing.
Their clients want to feel in control, visualize, and personalize the construction process. The app not only improved the company’s construction progress monitoring but also connected consumers with the workers who build their dream homes.
The workers, typically the construction manager, take pictures and videos on the job site and mark tasks as ‘ready’ or ‘in progress.’ Based on these, the app calculates the percentage of project completion. The photos and project status are promptly sent to the client; push notifications prevent them from missing the updates.
Construction managers and workers also found it handy to keep permits at hand on their mobile devices and easily track team members’ availability.
2. Solutions Improving Communication, Collaboration, and Management
The ability to communicate and share data from various sources among multiple agents is one of the persistent trends in construction technology.
However, growing building complexity and expanding numbers of stakeholders and players require better cooperation, driving the demand for better communication technology in construction industry contexts.
Construction management software (CMS) has become indispensable for many construction companies as it stores data, blueprints, and documents in one place and allows access to them from anywhere. These solutions help manage project timelines and resources and even anticipate potential challenges, facilitating prompt corrective measures.
The global CMS market, valued at $15.7 billion in 2024, is expected to grow at a CAGR of 10.1% and approach $31 billion by 2031. Autodesk, Bentley Systems, and Trimble are some of the leading CMS vendors.
Cloud technology allows secure and affordable storing of massive amounts of information, making it instantly accessible for connected devices or data analysis platforms. As a result, cloud computing and mobile apps are replacing legacy software on computers in the back office.
Cloud-based solutions ensuring a seamless connection between back offices and workers in the field and real-time inputs of critical project data are particularly appropriate for managing geographically dispersed equipment and personnel. Users can access construction software at any time and location.
For example, instead of going back to the office to enter important data into the firm’s ERP, a person in charge can do it conveniently on site and make the information immediately accessible to all authorized people.
Digital asset management (DAM) software is another relatively new building technology trend. DAM systems designed for the AEC sector help teams manage, organize, and share digital assets, such as documents, images, and videos.
Document workflow management software helps improve collaboration with contractors and mitigate field-to-office miscommunication issues. Digital construction forms and automated workflows replace manual tasks and paper-based documents.
Centralized access to comprehensive project documentation helps streamline project workflows, ensure consistency in branding, and speed up the creation of winning proposals.
Online project collaboration software also proliferates. Cloud-based solutions connect and facilitate simultaneous task completion and decision-making by architects, suppliers, building product manufacturers, building inspectors, and subcontractors. This saves time on numerous negotiations and reduces miscommunication mistakes.
An all-in-one cloud-based platform can integrate all construction firm’s operations, facilitate the management of projects, partners, labor, and assets, provide actionable insights, and create a digital backbone for the construction process from start to finish. AI and ML integration may help optimize inventory and resource allocation and enhance predictive logistics.
Instead of purchasing off-the-shelf software and paying monthly fees for modules you are not going to use, your company can order a custom solution. It will be designed considering your unique requirements or innovative construction methods.
Cloud computing also enables other recent trends in construction technology, such as IoT and virtual design and construction (VDC) – the use of virtual environments to engineer and visualize the construction of structures before they are built.
3. Building Information Modeling (BIM) & Digital Twins
BIM is a prime example of this digital innovation in construction technology.
This software enables collaboration on digital representations of a building’s physical and functional aspects before a project starts. Creators can add layers to interactive 3D models (e.g., construction specifications), simulate construction procedures, and more.
Currently, 5 BIM dimensions are distinguished:
Dimension | BIM feature | Description |
Geometry | 3D | The visualization of the three geographical dimensions (x, y, z) of a building structure enables stakeholders to collaborate on modeling and solving typical structural problems. |
Time | 4D |
The consolidation and visualization of information on
|
Money | 5D |
These features enable project promoters and owners to
|
Sustainability and energy- efficiency | 6D (integrated BIM) |
These features consolidate information necessary for making a building self-sustainable and energy-efficient, including each component’s manufacturer, installation date, maintenance schedule, configuration, energy requirement, and decommissioning details. 6D BIM helps
|
Facility management | 7D |
7D BIM collates in a model all information related to operations and facility management throughout a building’s lifecycle for future use.
|
AEC professionals can collaborate on a shared model even while in the field. Key vendors can also integrate 3D models of components to ensure they fit and work well before construction begins. All changes and updates to the project are immediately visible to all stakeholders.
The comprehensive visualization facilitates collaboration and planning out each project phase. BIM tools also facilitate document management during the planning, design, construction, operation, and maintenance of a building.
As construction projects become more complex, BIM tools play a pivotal role in streamlining processes. Construction firms also increasingly combine BIM with modular construction and prefabrication to maintain budgets and tight construction schedules.
The expansion of building lifecycle management, industry standards, certifications, and legislative mandates have made BIM a de facto “license to operate,” particularly in new build construction.
These factors partly explain the notably high popularity of BIM compared to other new technology used in building construction. For example, nearly 45% of European architects were BIM users in 2023, although the percentages varied by country and depended on the company size: the bigger the company, the more likely they were to embrace BIM practices. This trend will likely persist as construction firms increasingly recognize their value.
Autodesk’s Revit, BIM 360, and Navisworks are basically the standard in virtual modeling.
The global BIM market size, estimated at $9.4 billion in 2024, is projected to grow at a CAGR of 16.6% and approach $17.5 billion in 2028.
However, it’s worth mentioning that BIM adoption amongst contractors is lower than among architects (e.g., 35% of contractors vs. 75% of architects in the Netherlands). The usage of BIM features beyond 3D also remains limited. This suggests untapped potential for further technological exploration and innovation in construction industry sectors.
BIM is one of the fastest proliferating digital technologies in construction
BIM also supports the latest trends in construction technology: digital twins, AI, and mixed realities. A BIM system integrated with IoT devices collecting real-time data gives stakeholders enhanced control over a building’s design, construction, operation, and maintenance.
A digital twin is basically an accurate virtual representation of a physical object or system. For example, once Onix created a digital twin that not only looks like the MaXx-D SYNC Mk2 Flashlight but also simulates its functions. Users can examine the flashlight from every angle, test its features, and understand its mechanics without holding a physical item.
Onix’s experience with digital twins – another latest technology used in building construction
Learn more: A Deep Dive into Product Digital Twin Development
Digital twin technology uses sensors, drones, and IoT applications to gather data on an existing building or one under construction. AI software, advanced analytics, and ML algorithms process that data to create and update a dynamic digital replica of the building in real time.
Digital twins can be used to create data-rich as-built drawings, improve project scheduling, monitor a project’s status throughout all phases, and simulate, predict, and guide decisions.
3. Augmented Reality (AR) and Virtual Reality (VR)
AR, which superimposes computer-generated images on a live view on a device’s screen, and VR, which fully emerges wearers of special headsets in simulated environments, are relatively new trends in construction technology.
AR applications use markers, such as QR codes, architectural drawings, or geolocation, to overlay BIM models, installation and safety instructions, and more.
For example, the image of a completed project can be overlaid on a blueprint so that the client can visualize it during discussions, pretty much like Onix’s AR mobile app superimposed a 3D model of our headquarters on a brochure.
Onix has vast experience with AR – an exciting new technology in construction industry
The presentation of BIM data through an AR visual platform can foster coordination and collaboration between consultants, designers, and construction teams.
Overlaying the images of buildings, systems, and their surroundings on physical site views, users can visualize projects, simulate architectural or structural changes, receive feedback, and facilitate design improvements.
AR integrated into head-up displays in safety goggles and hard hat visors has enormous potential. Workers will be able to check project documents, guides, and checklists, access critical information about equipment, see hidden structures or 3D models, and identify hazards and ways to avoid them while keeping their hands free to perform tasks.
Trimble XR10 with Microsoft HoloLens remains a great example of a hard hat solution.
There’s evidence that AR cut the completion time of simple pipe assembling by 50% compared to drawings and by 9% when the task was complex and closer to reality. Workers assisted by AR also made 50% fewer errors than those who used drawings.
Paired with BIM, VR also facilitates collaboration between the architects and other stakeholders. First, they create a building model with BIM and then literally walk through and around its twin in virtual reality.
It’s a low-stakes way to visualize an entire project, eliminate change orders, and detect clashes before construction. The team members can work together on a project regardless of their physical location.
Read also: Virtual Reality Meetings: Benefits, Use Cases, and Pro Development Tips
Immersive visualization enables architects to present their designs and firms – to showcase property for sale or under construction. Managers, supervisors, inspectors, owners, or tenants don’t even need to be physically present to take a walkthrough of a building.
Here is Onix’s example of such visualization. VR Apartments 2021 not only immerses users in their would-be home atmosphere but also allows them to shape it using in-app interfaces.
While users explore apartments and houses, view objects from different angles under day and night light, and interact with them to evaluate utility, they can also choose colors and materials for the interior elements and see how they work out!
Learn more: Why Construction Companies Can’t Ignore Virtual Reality
It’s also practical to utilize this new technology in construction safety, equipment and machinery operation, and systems installation training. Simulated environments expose trainees to various field scenarios and possible hazards they have to handle while staying safe.
Learn more: Training in Virtual Environments: 360° Video vs. Full VR
Onix also develops educational applications for the construction industry. For example, below, you can see a VR simulation for VR/MR platforms. The project for heavy equipment operators included the creation of instructions for checking the machines’ condition, control of the machines, the views from the cockpit, and a testing system facilitating certification.
In 2022, Onix’s VR developers created a series of immersive learning experiences for an American EdTech company. The simulations provide hands-on training, albeit in the virtual world, to master real-life skills ranging from reading construction drawings to specific jobs like carpentry or plumbing. A virtual coach shows how to perform essential tasks, gives instant feedback on a trainee’s actions and answers, and evaluates their performance.
Both VR and AR improve learning outcomes. Moreover, the application of new technologies in construction education and training appeals to the younger generation of construction workers.
5. Advanced Use of Construction-related Data
Construction businesses generate oceans of data, including project specifications and financial and employee records, that can be used to uncover hidden trends, correlations, anomalies, or behavior patterns. This provides the basis for data-driven decision-making, AI, and automation systems, whose role in the AEC industries is growing.
For example, historical project data can be used in construction planning and scheduling, cost estimation, predictive logistics, etc. Forecast models allow project managers to determine the feasibility of time frames.
Onix’s recent AI project, an expert system using algorithms and geospatial tools, helps assess land development feasibility. The system divides a terrain with a grid, calculates gradients, and automatically identifies flat areas optimal for construction. It also evaluates sites’ connectivity by measuring the distance to roads and utilities.
AI and ML are expected to be used more frequently in conjunction with BIM, digital twins, sensors, wearables, cameras, laser scanners, and other latest technology in the construction industry.
The AI in construction market is anticipated to grow at a CAGR of 20% from 2023 to 2032. The growth of AI solutions for construction projects is driven by their ability to improve decision-making, automate processes, optimize project scheduling, resource allocation, and risk management, and enhance safety.
Balancing the trade-off between bulk-buying materials at lower prices, considering associated increased storage and transport complexities, and buying smaller amounts, potentially paying more or facing delays, is a persistent challenge in the construction industry. An integrated supply chain system offers one way to tackle it.
This could mean setting up a unified vendor platform that includes all stakeholders. Intelligent use of data and dynamic algorithms is key. Dynamic algorithms will use large datasets covering the availability, quality, and pricing of materials and monitor the demand, productivity, and skills of the labor force to suggest optimized orders and schedules.
Here are more examples of how AI and ML can benefit construction firms:
- Generative AI can create multiple design options based on specific criteria and constraints and considering the mechanical, electrical, and plumbing systems.
- The analysis of weather, traffic, and community and business activity data can help determine the most problematic areas and optimal phasing of construction activities.
- By analyzing the productivity of the workforce and equipment, project teams may be able to predict potential delays, fatigue, and overall project time and cost overruns.
- AI-driven automation can take over repetitive tasks, improving the productivity and safety of the workforce.
- AI using geolocation data helps improve equipment logistics and availability of spare parts and avoid downtime.
- Using photos, recognition technology, and geolocation, construction sites can be monitored to identify inadequate PPE or hazards and immediately alert the worker and safety manager via their smartphone or a wearable device, preventing accidents.
- The same method can help with surveillance, real-time theft protection, and work progress monitoring, improving accountability and efficiency on construction sites.
- Sensors on machines help track their active and idle time; this information helps firms decide whether to buy or lease such equipment and determine the most sustainable fuel use.
- Sensors embedded on objects and in workers’ apparel allow tracking their movement and usual routes, providing insights for job site optimization to maximize efficiency.
Using ML algorithms, AI can check the quality of excavation, plumbing, and electrical work and the compliance of the installed systems with the initial models and plans.
Traffic stress and bridge flexing data can be fed back into BIM systems to plan maintenance activities.
AI and ML are also integral to the most impressive emerging technologies in construction: self-operating and autonomous construction equipment, robots, and drones.
Drones and robotics have the potential to improve construction site safety and efficiency dramatically.
For instance, aerial drones are gaining widespread use as a surveying tool. They help quickly map extensive areas, generating valuable aerial heat maps and thermal images.
Drones can also track construction progress and perform inspections, which is especially handy with large or remote building sites, and perform hazardous tasks. The advancement in drone software provides real-time data for better-informed decisions.
In conjunction with AI, drones are expected to monitor equipment depreciation and manage moving construction machinery more efficiently.
Drones were already utilized on 55% of projects in 2022, with large contractors demonstrating higher usage (67%) than small contractors (9%). The use of drones in construction is a market worth roughly $4.8 billion in 2024. By 2030, this demand will generate some $6.2 billion.
Robots are taking on repetitive, labor-intensive, hazardous, and time-consuming tasks like bricklaying, material handling, and demolition, enhancing process speed and precision and reducing risks, fatigue, and labor costs.
The global construction robot market is projected to grow at a CAGR of 19% from 2024 to 2033.
Over 70% of construction equipment manufacturers will offer robotic solutions for earthmoving, excavation, and grading. The use of mobile robots for material transportation and logistics on construction sites will likely grow by 40% from 2023.
Besides closing the workforce gap and improving safety, early adopters of robotics in the construction industry can expect waste reduction and enhanced productivity. Let’s summarize these and other positive results of innovative construction technology implementation.
How Technology Is Changing the Construction Industry
Here are some benefits companies can expect from implementing new digital technology in construction industry sectors.
Higher Efficiency
BIM, site sensors, predictive analytics, and other new technologies increase efficiency by helping create more predictable build projects, prevent construction issues, and reduce downtime and material waste.
AR technology used in construction projects is known to boost productivity by speeding up the mapping of construction information from 2D drawings to the real world. For instance, it reportedly accelerated issue identification during a pipeline design review by 41.7% compared with a traditional analysis of photos.
Other case studies on using AR and BIM in construction inspection showed that AR app integration resulted in a 40% increase in task efficiency for on-site workers, while interoperability with the existing design software streamlined revisions, reducing the time for changes by 25%.
Automation that streamlines workflows, autonomous construction equipment, and robots that perform tasks faster and with higher precision help projects stay on schedule and within budget and can drastically reduce project timelines.
Cost Reduction
VDC helps cut down on costly reworks of faulty or incorrect builds, and financial data analytics facilitates better budgeting and cost management, identifying areas where expenses can be minimized without compromising quality.
As construction industry costs are rising, BIM, drones, and AR are becoming essential to cost management as they enhance precision and efficiency.
By automating tasks, construction companies decrease not only labor costs and waste but also reduce workplace injuries and ensure compliance with safety regulations, which lowers insurance costs.
Enhanced Safety
In 2022, the American construction industry saw more fatalities than any other industry sector: 1,069 construction professionals died while working, i.e. 9.6 per 100,000 full-time workers.
Many hope to reduce construction worker injuries and deaths by using robotics, drones, and AI-powered safety monitoring tools using IoT and wearables data.
For instance, drones survey and inspect locations without putting workers in harm’s way. There was a 55% increase in safety standards on construction sites employing drones.
AR/VR technology used in construction industry education and training provides workers with realistic scenarios and safe virtual environments that enhance their understanding of hazards, precision and other skills, and reactions to accidents. For example, an experiment showed that participants equipped with AR achieved a 90% awareness rate of potential hazards, compared to 48% without AR.

Ready to get the most out of your business by leveraging AR and VR technology?
Mobile apps also provide construction managers and workers with tools to do their jobs more safely. For example, Safesite claims to reduce workplace incidents by up to 57%.
Read also: Maritime Safety App Development
Environmental Impact
Automated and digitized back office processes and optimized logistics and supply chain management lead to lower carbon emissions and waste. Energy-efficient systems designed, implemented, and run with BIM, VDC, AI and ML systems also help meet sustainability regulations and reduce operational expenses and the need for repairs.
Read also: Top Sustainability Trends for 2025: Key Innovations
However, realizing the full potential of new technology in construction requires overcoming significant challenges.
Challenges and Barriers to Emerging Technology in Construction
While leaders in the healthcare, education, commerce, travel, entertainment, finance, maritime industries, and even art and culture actively invest in digitalization, data-driven products, and immersive experiences, AEC businesses have been slower at adopting modern technology in construction industry contexts.
Here are some of the factors that hinder innovation in construction technology:
Financial Concerns
The adoption of AI and other new technology in building construction is often hampered by the high cost of investment and operation. The expenses may include hardware, software, equipment, specialized expertise, infrastructure, workforce training, operational costs, regular updates and repairs, and more. These may be prohibitive for small- and medium-sized companies and emerging markets.
Skills Gap
Some construction technology trends require specialized knowledge that the current workforce lacks. Workers need ongoing education and training to operate and maintain AI and ML systems, drones, and robots. The need to invest in upskilling employees or hiring specialized talent can slow down the adoption and scare off companies with limited resources.
Unpreparedness
A company’s willingness to embrace innovative construction methods doesn’t always mean it is ready. For example, data obscurity, obsolete systems, and outdated regulatory frameworks remain significant hurdles for many firms.
Software installations and integration of new tech into business and construction processes can often be disruptive. Companies must carefully assess underlying priorities, prepare properly, and only opt for innovation in construction areas that will yield the highest benefit.
Resistance to Change
The mere conservative nature of the industry, one of the oldest, may resist new trends in construction technology. Attempts to innovate can meet resistance from both workers and stakeholders.
Employees may perceive the most up-to-date processes and techniques as too complex or ‘fads’ and automation as a threat to their job security. Stakeholders may resist change due to concerns over costs or perceived low efficiency of some emerging technologies in construction contexts.
Technology Limitations
Despite the significant potential and proven benefits of construction robotics, AR, VR, AI, ML, or any new technology used in building construction, some limitations remain.
For instance, current robotic systems may struggle with obstacles or adverse weather conditions. Moreover, it can be challenging to ensure compatibility between these systems, especially when they come from different vendors.
Regulatory Hurdles
Regulatory frameworks that lag behind technological progress hinder the adoption of the latest technology in construction industry. For instance, firms may face restrictions on where and how they can use drones. Building codes may not yet account for AI-driven solutions.
Data security and privacy concerns also aggravate as multiple integrated systems and devices driving innovation in construction industry processes may make companies and individuals vulnerable to cyberattacks.
Final Thoughts
Most of the construction industry technology trends discussed in this article can be tied to making the industry
- faster (e.g., thanks to collaboration instruments or AR apps)
- safer (e.g., due to VR technology used in construction training)
- better (e.g., ML-powered quality control and robots’ accuracy)
Interestingly, these themes also tend to result in better environmental sustainability and cost savings, which should accelerate the adoption.
New technologies raise hopes for AEC businesses amid labor shortages, increasingly stringent safety regulations, soaring material costs, economic uncertainty, and other challenges. The ability to build faster and smarter and a reputation for technological innovation makes a company more competitive.
Construction businesses and AEC software developers that want to gain a competitive advantage and appeal to increasingly demanding clients need to invest in innovation and keep their eyes open for future trends in construction technology.
Onix is just that kind of company! We are an award-winning web and mobile development agency with experience in emerging technologies like AR, VR, and AI/ML. Just book a free consultation to discuss your business needs and construction innovation ideas!
FAQ
What type of digital technology is trending in the construction industry?
There current digital technology trends in the construction industry include:
- Cloud-based communication and collaboration solutions
- Mobile construction apps
- BIM and digital twins
- AR and VR applications
- Big data, AI, and ML
- 3D printing
- Robots and drones
- IoT
- Wearable devices
- Blockchain technology
What are the most popular types of construction apps?
- Computer-aided design, drawings, and collaboration apps
- Construction management tools
- Construction materials calculators
- Material delivery apps
- Construction site inspection apps
What is the impact of IT innovations in the construction industry?
The use of new technology in construction projects results in the following improvements:
- Streamlined communication and collaboration between back-office and field workers, reduced errors and higher productivity
- More flexible and accurate documentation and record-keeping
- Greater flexibility, efficiency, and transparency of the construction workflows
- Increased visibility, accountability, and safety on job sites
- Reduction in paperwork, calls, emails, trips, non-compliance instances, and mistakes that lead to rework
- Reduced construction time
What are future trends in construction technology?
As the sector will likely prioritize efficiency, safety, and sustainability in the coming years, we expect construction industry trends to include creative, technologically advanced solutions that will make construction faster, more cost-efficient, and environment-friendlier and the buildings – smarter and more energy-efficient. You will likely see more green technology trends and developments in autonomous heavy equipment and building materials.

Never miss a new blog post from us!
Join us now and get your FREE copy of "Software Development Cost Estimation"!
This pricing guide is created to enhance transparency, empower you to make well-informed decisions, and alleviate any confusion associated with pricing. In this guide, you'll find:
Factors influencing pricing
Pricing by product
Pricing by engagement type
Price list for standard engagements
Customization options and pricing
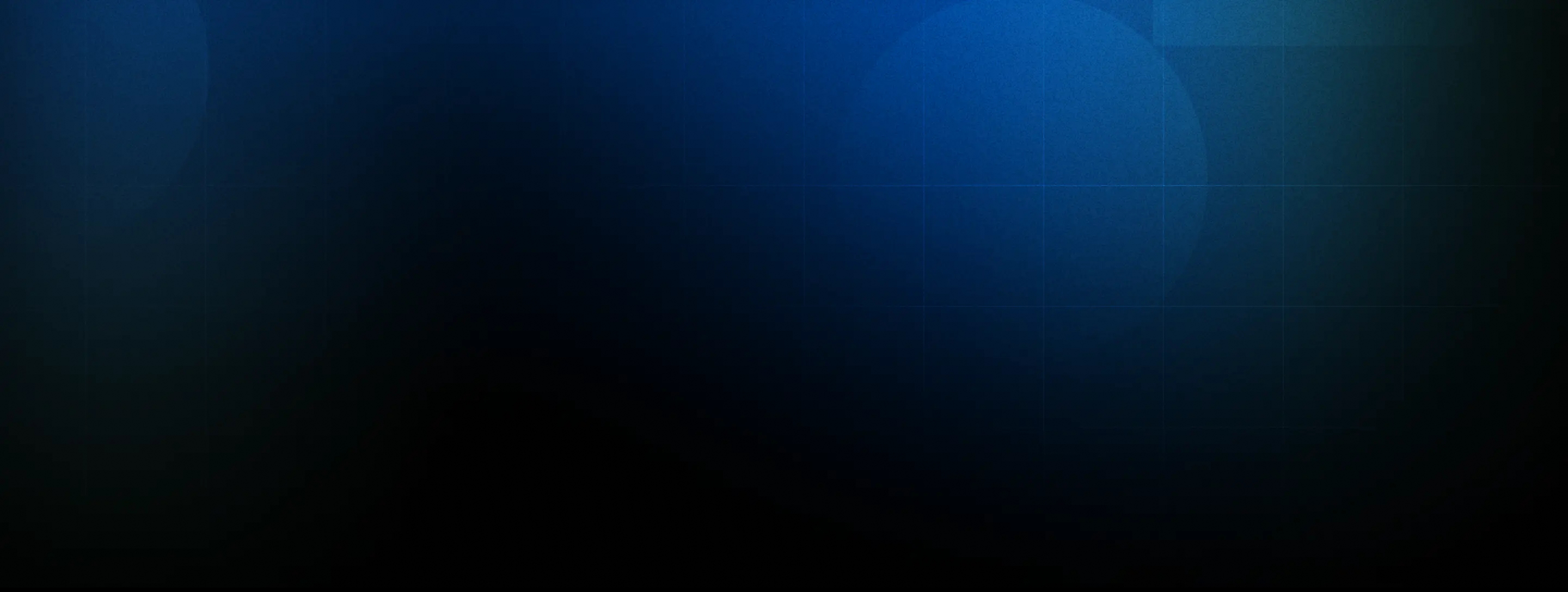